What is DTF Printing? Introduction of Basic Knowledge
- Papipapi Papiarea
- Apr 22, 2023
- 7 min read

DTF printer, which appeared as the latest transfer printer, has recently become a hot topic in the wear printing industry.
In this article, DTF TORONTO, a supplier of equipment and materials for wear printing, will explain the basic information of the latest technology DTF from the viewpoint of a heat transfer professional.
*The following are our DTF printers (SUPREME HD)



What is DTF Printing?
New technology DTF printers are expanding rapidly!
DTF printer, which appeared as the latest transfer printer, has recently become a hot topic in the wear printing industry.
"DTF" stands for "Direct To Film" and is responsible for the output of the DTF printer.
Specifically, DTF printers are water-based inkjet printers equipped with CMYK inks and white inks, which are characterized by full-color printing on film (PET film) and producing hot-melt transfer sheets (marks).
Printing is completed by hot pressing the produced transfer sheet on wear, etc., but this transfer printing method "DTF printing" is attracting attention.
DTF printing (system) is a transfer sheet (mark) production system using a DTF printer.
In fact, overseas shipments of DTF printers, which is this new technology, seem to be rapidly expanding.
About the DTF Printing System
Without version! Free design! Full color! Fully automatic, small lot to mass production, high quality mark at low price.
The method of making transfer sheets by DTF does not require any troublesome work at all.
Moreover, since it is fully automatic and can produce a large amount of transfer sheets (marks) with high quality and low cost, it can be said to be an epoch-making printing system.
In addition, since it can be done without plate making (plate cost), it is a printing method that can correspond to small lot.
Since it is full color and has no design restrictions, it is possible to print even a design that was avoided in the past, and it will dig up potential print demand.
And it is expected that printing speed and coloring accuracy will continue to improve in the future, and expectations will only increase for its wide range of possibilities.
However, in order for DTF printing to be firmly positioned as a fully automatic printing method with high quality and durability, the key to this is that DTF printers have "reliability and operability as equipment".
It is easy to imagine that the ink film powder, which is the material, is still sufficiently low-cost at the present time, and that the quality of the ink film powder will be further improved and improved.
DTF printers are the most remarkable printing equipment and printing method right now.
DTF Printers and DTF Printing Systems
Water-based Inkjet & Powder (Hot Melt Binder) Improves Productivity
The DTF printing system consists of equipment and materials.
[Device]
DTF Water-Based Inkjet Printer
Binder fixing machine (shaker/oven)
Smoking machine
*DTF printers can be roughly divided into "separate connected type" and "integrated integrated type" between the printer and the binder fixing machine.
[Material, Consumables]
Film (PET film)
Ink (Waterborne Pigment Ink ; CMYK & White Ink)
Powder (Hot Melt Binder)
Printed on ● film (CMYK+White)
The process is first printed on film with a DTF inkjet printer.
After all, the key to the system is ink.
Our premium inks provide high color density, wide color gamut, and excellent saturation.
After printing with CMYK ink, white ink is printed in a form that covers only the entire image, and powder (hot melt binder) is applied.
Apply powder to ● image part → Melting → Curing and drying → Transfer sheet
The powder is then sprinkled evenly, and then the excess powder is removed (reusable), leaving only the image with the powder.
After that, the powder is melted by heat treatment in the binder fixing machine, then hardened and dried to complete the transfer sheet.
Since the production of the transfer sheet is completed in the series of processes so far, it can be said that it is an epoch-making method.
Even fine designs and letters can be produced in small lots with high quality.
Moreover, rework and loss due to mistakes in scrap removal work are minimized, contributing to productivity improvements with significant cost cuts.
In addition, if a binder fixing machine (shaker) is used, powder is automatically applied only to the ink part, so plate making is not required, and the time and effort of "removing scum" and "retack" are not required to peel off excess parts.
Instead of a binder fixing machine (shaker), it is also possible to apply powder by hand and bake it.
The method is to cut the sheet after printing, apply the powder, and use the curing oven.
The printing process on the material such as the clothing subject to processing is only done by pressing the transfer sheet with a heat press machine, and the printing is completed by peeling the film.


About the Production Flow of DTF Printing
[Creating the design]
Create a design using graphics software such as Illustrator or Photoshop, and use the image format necessary for operating RIP software (e.g., png format, etc.).
RIP (software)It can also convert image data to print data, and this RIP can print white ink on top of CMYK colors.
[Printed]
Print the design on film. After printing the image with CMYK ink, white ink is printed on the CMYK ink so that only the entire image is covered.
[Powder (adhesive) coating]
To apply powder to the white ink area, sprinkle the powder evenly on the printed film and shake off the excess powder.
[Heating and melting powder (adhesive) & curing / drying]
After the powder is melted by heat treatment, hardened and dried to complete the transfer sheet.
[Crimping by heat press machine]
Using a heat press machine (or iron), the transfer sheet is crimped to the material. Finally, the film is peeled off and the print is completed.
Significant Advantages of DTF Printing Transfer Sheet Film
DTG (Direct-to-garment) printing method.
The advantage of "no platemaking" is similar to that of DTG (Direct to Garment), but instead of directly printing clothes like DTG, there are many advantages of DTF printing once on film.
In particular, for the wide range of print objects and high workability, and other printing methods.
DTG is a method of printing directly on clothing, and for dark-colored fabrics and polyester fabrics, the condition is that the fabric is coated (pretreated) with a liquid called a pretreatment agent.
On the other hand, DTF printing does not require such "pre-processing".
In addition, in the case of DTG, traces of pretreatment agent and odor remain, so it may be necessary to care for it, and it takes time and effort.
Also, it is not necessary to change the type or method of the sheet depending on the material material or color as in other transfer prints.
The fact that all DTF printing works on the same sheet is also one of the major advantages.
In addition, there is information that almost all DTG users purchase DTF printers overseas, and it is beginning to be expected that the number of DTF printers shipped will exceed DTG printers in the future.
Impact on the Wear Print Market
"One (1) press" to dark color, poly, nylon, etc. with "no pretreatment"! Low running costs make it an attractive print choice.
I mentioned earlier that DTF prints can be printed not only on white and light-colored fabrics but also on dark-colored fabrics without the need for "pretreatment like DTG". Moreover, the target material is not only cotton wear, but also polyester fabric, nylon product, cap, denim, enamel material, leather, nonwoven fabric (except some parts), etc. It is suitable for various kinds of fabrics /materials and applications, and it makes you feel the great possibility of printing. In addition, the cost of materials and consumables is incomparably lower than that of DTG and solvent transfer, which are the same inkjet methods.
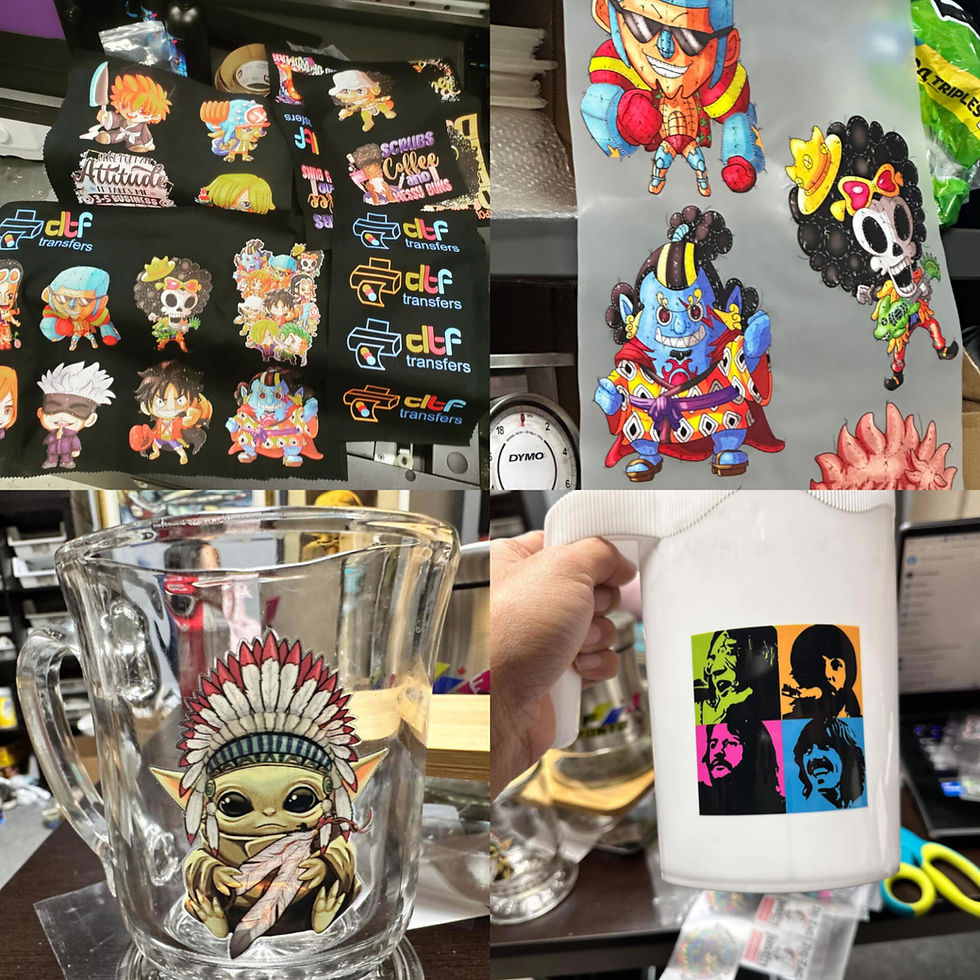
In addition, when you include significant reductions in labor costs that are difficult to quantify and visualize, productivity will have a profound impact on traditional cost perceptions.
Naturally, since it is a fully automatic and mass-production type as mentioned above, the impact on the entire print market will be immeasurable in the wear print industry rather than the original.
The Quality of DTF Prints
Apparel, sports and uniforms are no problem!
Wear print quality must be judged by friction degree, washing degree, and formaldehyde (formalin).
Our premium inks use are certified high-quality inks.
The safety and quality of powders (hot melt binders) are also inspected and verified before commercialization.
We recognize that it is possible to print not only on quality-oriented apparel products and sportswear uniforms that require durability, but also on caps, gloves, socks, enamel bags, small article pouches, etc. At our company, we will proceed with preparation so that we can propose such various print examples.
About DTF TORONTO
We are an authorized supplier of equipment and materials for wear printing, and we will give you the best advice unique to heat transfer professionals.
Wear print quality must be judged by friction degree, washing degree, and formaldehyde (formalin).
At least, we do not sell models and materials that do not meet the standard.
In particular, we conduct thorough verification of transfer temperature and number of presses that have a significant impact on the degree of washing.
We do not only transfer DTF to the body under normal press conditions, but also test under various conditions such as extremely low press temperature as 100°C or one press, and then wash multiple times to check the durability, etc.
And in our company, solid printing on film and DTF transfer without plate making and scum removal, and the finish similar to silk screen printing and rubber transfer was reproduced.
In addition, we have tried DTF transfer to various materials such as nylon water repellent cloth, enamel, six-sided panel hat, synthetic leather such as PU, rain umbrella, coarse knitted products, etc., and continue to pile up detailed know-how.
We will continue to pursue quality improvement, ink cost reduction and printing speed improvement. Because DTF transcription is a new manufacturing method, such detailed verification becomes important.
We have a dedicated DTF shop where you can actually see, touch and experience DTF printers. If you are a wear printing company or planning to start a printing business who wants to be introduce a new manufacturing method with peace of mind, please contact us.
Call us: 647-822-4657
Email: dtftoronto.ca@gmail.com
We will give you the best advice unique to heat transfer professionals.



Follow our official social media accounts:
Tiktok: https://vm.tiktok.com/ZMYvnpenH/
Pinterest: https://pin.it/1Giu5dz
Comments